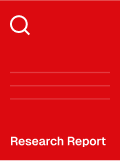
Encoders
Description
Global Encoders Market to Reach US$4.5 Billion by 2030
The global market for Encoders estimated at US$2.7 Billion in the year 2024, is expected to reach US$4.5 Billion by 2030, growing at a CAGR of 8.6% over the analysis period 2024-2030. Rotary, one of the segments analyzed in the report, is expected to record a 9.3% CAGR and reach US$2.6 Billion by the end of the analysis period. Growth in the Linear segment is estimated at 7.7% CAGR over the analysis period.
The U.S. Market is Estimated at US$701.0 Million While China is Forecast to Grow at 12.5% CAGR
The Encoders market in the U.S. is estimated at US$701.0 Million in the year 2024. China, the world`s second largest economy, is forecast to reach a projected market size of US$1.1 Billion by the year 2030 trailing a CAGR of 12.5% over the analysis period 2024-2030. Among the other noteworthy geographic markets are Japan and Canada, each forecast to grow at a CAGR of 4.8% and 7.8% respectively over the analysis period. Within Europe, Germany is forecast to grow at approximately 5.4% CAGR.
Global Encoder Market - Key Trends & Drivers Summarized
Why Are Encoders Essential in Modern Automation and Control Systems?
Encoders are critical components in automation, robotics, and precision control systems, enabling accurate position, speed, and motion feedback for various applications. By converting mechanical motion into electrical signals, encoders provide real-time data that is essential for controlling machinery, robotics, conveyors, and motors. Common types of encoders include rotary, linear, optical, and magnetic encoders, each suited to different requirements for accuracy, durability, and environmental resilience. Industries such as manufacturing, automotive, aerospace, and healthcare rely heavily on encoders to ensure precise control over automated processes, improving productivity, accuracy, and safety.
In industrial automation, encoders help monitor motor positions and speeds, providing data to control systems that maintain accuracy in high-speed and complex operations. Encoders are especially critical in robotics, where precise movements and positioning are required to execute tasks with high precision. With the rise of Industry 4.0 and smart manufacturing, encoders are becoming indispensable, providing the real-time feedback necessary for enhanced automation and predictive maintenance, ultimately optimizing equipment performance and reducing downtime.
How Are Technological Advancements Shaping the Encoder Market?
Technological advancements are enhancing the performance, durability, and versatility of encoders, making them more adaptable to various applications and environments. One of the most significant developments is the rise of optical and magnetic encoders, which offer high accuracy, immunity to environmental factors, and longer operational life. Optical encoders, for example, use light patterns to detect position, delivering exceptional resolution and accuracy, which is critical in high-precision applications like CNC machining, semiconductor manufacturing, and robotics. Magnetic encoders, on the other hand, are durable and can operate effectively in harsh conditions, including exposure to dust, moisture, and vibrations, making them ideal for heavy-duty applications.
The integration of wireless and IoT capabilities is further transforming the encoder market, enabling remote monitoring and data transmission. IoT-enabled encoders allow real-time data collection, supporting predictive maintenance and operational insights that help avoid unexpected machine failures. Miniaturization is also a key trend, particularly in the medical device and consumer electronics sectors, where compact encoders are essential to fit within small, intricate designs without compromising performance. Additionally, advancements in high-resolution encoders are supporting the demands of emerging technologies like autonomous vehicles and robotic surgery, where precise motion control is crucial. Together, these technological advancements are expanding the applications and effectiveness of encoders, supporting their use across diverse and complex environments.
What Are the Key Applications of Encoders?
Encoders are used across various industries where precise measurement of position, speed, and direction is essential for operational accuracy. In the manufacturing sector, encoders play a vital role in controlling motorized systems in applications such as conveyor belts, packaging, CNC machines, and robotic arms. Encoders provide critical feedback on motor position and speed, enabling efficient control of automated machinery and ensuring precision in high-speed manufacturing processes. In the automotive industry, encoders are used in vehicle control systems, including steering, braking, and throttle systems, where they provide real-time position data to optimize vehicle performance and safety.
In robotics, encoders are indispensable for motion control, supporting tasks that require fine-tuned movements, such as assembly, welding, and inspection. The aerospace and defense industries also rely on encoders for accurate positioning in applications like navigation systems, radar, and missile guidance. Additionally, in medical technology, encoders are integrated into equipment like MRI machines, robotic surgery systems, and infusion pumps, where precise control over positioning and motion is critical. These applications highlight the versatility of encoders, enabling reliable, high-precision control across industries where accuracy and efficiency are paramount.
What Is Driving Growth in the Encoder Market?
The growth in the encoder market is driven by the increasing demand for automation and precision control, advancements in encoder technology, and the expansion of IoT-enabled smart systems. As industries adopt automation to enhance productivity and reduce costs, the need for high-performance encoders is rising to ensure the accuracy and reliability of automated systems. The shift towards smart factories and Industry 4.0 has further spurred demand for IoT-enabled encoders, which provide real-time data for monitoring and predictive maintenance, helping to optimize equipment utilization and minimize downtime. Technological advancements, such as the development of high-resolution optical and magnetic encoders, are also supporting market growth by enabling more precise measurement and expanding application possibilities. The increased focus on robotics, particularly in logistics, manufacturing, and healthcare, is driving demand for encoders that can support intricate, precise movements. Additionally, the automotive industry’s focus on safety and automation, including the development of electric and autonomous vehicles, is boosting demand for encoders to provide the necessary feedback for accurate control systems. Environmental and regulatory requirements are encouraging the adoption of energy-efficient and durable encoders, particularly in sectors where equipment must operate reliably in harsh conditions. Together, these factors—growing automation, technological advancements, IoT integration, and the expansion of precision-driven industries—are driving robust growth in the encoder market, establishing these devices as essential components for modern automation and control systems.
SCOPE OF STUDY:The report analyzes the Encoders market in terms of units by the following Segments, and Geographic Regions/Countries:
Segments:
Type (Rotary, Linear); Technology (Optical, Magnetic, Other Technologies); End-Use (Industrial, Automotive, Consumer Electronics, Food & Beverage, Medical, Other End-Uses)
Geographic Regions/Countries:
World; United States; Canada; Japan; China; Europe (France; Germany; Italy; United Kingdom; Spain; Russia; and Rest of Europe); Asia-Pacific (Australia; India; South Korea; and Rest of Asia-Pacific); Latin America (Argentina; Brazil; Mexico; and Rest of Latin America); Middle East (Iran; Israel; Saudi Arabia; United Arab Emirates; and Rest of Middle East); and Africa.
Select Competitors (Total 48 Featured) -
- Baumer Group
- Dynapar Corporation
- Faulhaber Group
- Heidenhain GmbH
- IFM Electronic GmbH
- Maxon Motor Ag
- Micronor Inc.
- Nidec Corporation
- Omron Automation
- Pepperl+Fuchs
- Pilz GmbH Co. Kg
- Posic
- Posital-Fraba Inc.
- Renishaw PLC
- Rockwell Automation Inc.
- Sensata Technologies
- Siko GmbH
- Turck Banner Singapore PTE Ltd
- US Digital
- Wachendorff Automation GmbH +Co Kg
Please note: Reports are sold as single-site single-user licenses. Electronic versions require 24-48 hours as each copy is customized to the client with digital controls and custom watermarks. The Publisher uses digital controls protecting against copying and printing is restricted to one full copy to be used at the same location.
The latest version of Adobe Acrobat Reader is required to view the report. Upon ordering an electronic version, the Publisher will provide a link to download the purchased report.
Prior to fulfillment of an order, the client will be required to sign a document detailing the purchase terms for a publication from this publisher.
Table of Contents
- I. METHODOLOGY
- II. EXECUTIVE SUMMARY
- 1. MARKET OVERVIEW
- Influencer Market Insights
- Tariff Impact on Global Supply Chain Patterns
- Global Economic Update
- Encoders – Global Key Competitors Percentage Market Share in 2025 (E)
- Competitive Market Presence - Strong/Active/Niche/Trivial for Players Worldwide in 2025 (E)
- 2. FOCUS ON SELECT PLAYERS
- 3. MARKET TRENDS & DRIVERS
- Rapid Advancements in Industrial Automation and Robotics Drive Demand for Precision Encoders in Manufacturing and Processing
- Rising Adoption of Encoders in the Automotive Industry Supports Growth in Electric Vehicle (EV) and Autonomous Vehicle Applications
- Expanding Application of Encoders in Medical Equipment Boosts Demand for High-Accuracy Motion Control Solutions in Healthcare
- Growth in Aerospace and Defense Sectors Drives Market Demand for Robust Encoders with High Reliability in Harsh Environments
- Increased Integration of Encoders in Smart Factory and Industry 4.0 Initiatives Spurs Demand for Real-Time Monitoring and Control
- Rising Demand for High-Resolution Encoders in Consumer Electronics Supports Market Growth in Wearable Devices and Smartphones
- Technological Advancements in Optical Encoders Improve Accuracy and Durability, Enhancing Market Adoption in Precision Applications
- Expanding Use of Encoders in Renewable Energy Applications, Especially in Wind and Solar Power, Drives Market Demand
- Growing Demand for Encoders in 3D Printing and Additive Manufacturing Enhances Precision in Prototyping and Production Processes
- Rise in Demand for High-Speed Automation in Food and Beverage Industry Fuels Adoption of Encoders for Accurate Positioning
- Increasing Deployment of Encoders in Semiconductor Manufacturing Supports Growth in High-Precision Motion Control Applications
- Emergence of AI and Machine Learning in Motion Control Enhances Performance and Accuracy of Encoder-Based Systems
- 4. GLOBAL MARKET PERSPECTIVE
- TABLE 1: World Recent Past, Current & Future Analysis for Encoders by Geographic Region - USA, Canada, Japan, China, Europe, Asia-Pacific, Latin America, Middle East and Africa Markets - Independent Analysis of Annual Sales in US$ Thousand for Years 2024 through 2030 and % CAGR
- TABLE 2: World Historic Review for Encoders by Geographic Region - USA, Canada, Japan, China, Europe, Asia-Pacific, Latin America, Middle East and Africa Markets - Independent Analysis of Annual Sales in US$ Thousand for Years 2015 through 2023 and % CAGR
- TABLE 3: World 15-Year Perspective for Encoders by Geographic Region - Percentage Breakdown of Value Sales for USA, Canada, Japan, China, Europe, Asia-Pacific, Latin America, Middle East and Africa Markets for Years 2015, 2025 & 2030
- TABLE 4: World Recent Past, Current & Future Analysis for Rotary by Geographic Region - USA, Canada, Japan, China, Europe, Asia-Pacific, Latin America, Middle East and Africa Markets - Independent Analysis of Annual Sales in US$ Thousand for Years 2024 through 2030 and % CAGR
- TABLE 5: World Historic Review for Rotary by Geographic Region - USA, Canada, Japan, China, Europe, Asia-Pacific, Latin America, Middle East and Africa Markets - Independent Analysis of Annual Sales in US$ Thousand for Years 2015 through 2023 and % CAGR
- TABLE 6: World 15-Year Perspective for Rotary by Geographic Region - Percentage Breakdown of Value Sales for USA, Canada, Japan, China, Europe, Asia-Pacific, Latin America, Middle East and Africa for Years 2015, 2025 & 2030
- TABLE 7: World Recent Past, Current & Future Analysis for Linear by Geographic Region - USA, Canada, Japan, China, Europe, Asia-Pacific, Latin America, Middle East and Africa Markets - Independent Analysis of Annual Sales in US$ Thousand for Years 2024 through 2030 and % CAGR
- TABLE 8: World Historic Review for Linear by Geographic Region - USA, Canada, Japan, China, Europe, Asia-Pacific, Latin America, Middle East and Africa Markets - Independent Analysis of Annual Sales in US$ Thousand for Years 2015 through 2023 and % CAGR
- TABLE 9: World 15-Year Perspective for Linear by Geographic Region - Percentage Breakdown of Value Sales for USA, Canada, Japan, China, Europe, Asia-Pacific, Latin America, Middle East and Africa for Years 2015, 2025 & 2030
- TABLE 10: World Recent Past, Current & Future Analysis for Medical by Geographic Region - USA, Canada, Japan, China, Europe, Asia-Pacific, Latin America, Middle East and Africa Markets - Independent Analysis of Annual Sales in US$ Thousand for Years 2024 through 2030 and % CAGR
- TABLE 11: World Historic Review for Medical by Geographic Region - USA, Canada, Japan, China, Europe, Asia-Pacific, Latin America, Middle East and Africa Markets - Independent Analysis of Annual Sales in US$ Thousand for Years 2015 through 2023 and % CAGR
- TABLE 12: World 15-Year Perspective for Medical by Geographic Region - Percentage Breakdown of Value Sales for USA, Canada, Japan, China, Europe, Asia-Pacific, Latin America, Middle East and Africa for Years 2015, 2025 & 2030
- TABLE 13: World Recent Past, Current & Future Analysis for Other End-Uses by Geographic Region - USA, Canada, Japan, China, Europe, Asia-Pacific, Latin America, Middle East and Africa Markets - Independent Analysis of Annual Sales in US$ Thousand for Years 2024 through 2030 and % CAGR
- TABLE 14: World Historic Review for Other End-Uses by Geographic Region - USA, Canada, Japan, China, Europe, Asia-Pacific, Latin America, Middle East and Africa Markets - Independent Analysis of Annual Sales in US$ Thousand for Years 2015 through 2023 and % CAGR
- TABLE 15: World 15-Year Perspective for Other End-Uses by Geographic Region - Percentage Breakdown of Value Sales for USA, Canada, Japan, China, Europe, Asia-Pacific, Latin America, Middle East and Africa for Years 2015, 2025 & 2030
- TABLE 16: World Recent Past, Current & Future Analysis for Industrial by Geographic Region - USA, Canada, Japan, China, Europe, Asia-Pacific, Latin America, Middle East and Africa Markets - Independent Analysis of Annual Sales in US$ Thousand for Years 2024 through 2030 and % CAGR
- TABLE 17: World Historic Review for Industrial by Geographic Region - USA, Canada, Japan, China, Europe, Asia-Pacific, Latin America, Middle East and Africa Markets - Independent Analysis of Annual Sales in US$ Thousand for Years 2015 through 2023 and % CAGR
- TABLE 18: World 15-Year Perspective for Industrial by Geographic Region - Percentage Breakdown of Value Sales for USA, Canada, Japan, China, Europe, Asia-Pacific, Latin America, Middle East and Africa for Years 2015, 2025 & 2030
- TABLE 19: World Recent Past, Current & Future Analysis for Automotive by Geographic Region - USA, Canada, Japan, China, Europe, Asia-Pacific, Latin America, Middle East and Africa Markets - Independent Analysis of Annual Sales in US$ Thousand for Years 2024 through 2030 and % CAGR
- TABLE 20: World Historic Review for Automotive by Geographic Region - USA, Canada, Japan, China, Europe, Asia-Pacific, Latin America, Middle East and Africa Markets - Independent Analysis of Annual Sales in US$ Thousand for Years 2015 through 2023 and % CAGR
- TABLE 21: World 15-Year Perspective for Automotive by Geographic Region - Percentage Breakdown of Value Sales for USA, Canada, Japan, China, Europe, Asia-Pacific, Latin America, Middle East and Africa for Years 2015, 2025 & 2030
- TABLE 22: World Recent Past, Current & Future Analysis for Consumer Electronics by Geographic Region - USA, Canada, Japan, China, Europe, Asia-Pacific, Latin America, Middle East and Africa Markets - Independent Analysis of Annual Sales in US$ Thousand for Years 2024 through 2030 and % CAGR
- TABLE 23: World Historic Review for Consumer Electronics by Geographic Region - USA, Canada, Japan, China, Europe, Asia-Pacific, Latin America, Middle East and Africa Markets - Independent Analysis of Annual Sales in US$ Thousand for Years 2015 through 2023 and % CAGR
- TABLE 24: World 15-Year Perspective for Consumer Electronics by Geographic Region - Percentage Breakdown of Value Sales for USA, Canada, Japan, China, Europe, Asia-Pacific, Latin America, Middle East and Africa for Years 2015, 2025 & 2030
- TABLE 25: World Recent Past, Current & Future Analysis for Food & Beverage by Geographic Region - USA, Canada, Japan, China, Europe, Asia-Pacific, Latin America, Middle East and Africa Markets - Independent Analysis of Annual Sales in US$ Thousand for Years 2024 through 2030 and % CAGR
- TABLE 26: World Historic Review for Food & Beverage by Geographic Region - USA, Canada, Japan, China, Europe, Asia-Pacific, Latin America, Middle East and Africa Markets - Independent Analysis of Annual Sales in US$ Thousand for Years 2015 through 2023 and % CAGR
- TABLE 27: World 15-Year Perspective for Food & Beverage by Geographic Region - Percentage Breakdown of Value Sales for USA, Canada, Japan, China, Europe, Asia-Pacific, Latin America, Middle East and Africa for Years 2015, 2025 & 2030
- TABLE 28: World Recent Past, Current & Future Analysis for Optical by Geographic Region - USA, Canada, Japan, China, Europe, Asia-Pacific, Latin America, Middle East and Africa Markets - Independent Analysis of Annual Sales in US$ Thousand for Years 2024 through 2030 and % CAGR
- TABLE 29: World Historic Review for Optical by Geographic Region - USA, Canada, Japan, China, Europe, Asia-Pacific, Latin America, Middle East and Africa Markets - Independent Analysis of Annual Sales in US$ Thousand for Years 2015 through 2023 and % CAGR
- TABLE 30: World 15-Year Perspective for Optical by Geographic Region - Percentage Breakdown of Value Sales for USA, Canada, Japan, China, Europe, Asia-Pacific, Latin America, Middle East and Africa for Years 2015, 2025 & 2030
- TABLE 31: World Recent Past, Current & Future Analysis for Magnetic by Geographic Region - USA, Canada, Japan, China, Europe, Asia-Pacific, Latin America, Middle East and Africa Markets - Independent Analysis of Annual Sales in US$ Thousand for Years 2024 through 2030 and % CAGR
- TABLE 32: World Historic Review for Magnetic by Geographic Region - USA, Canada, Japan, China, Europe, Asia-Pacific, Latin America, Middle East and Africa Markets - Independent Analysis of Annual Sales in US$ Thousand for Years 2015 through 2023 and % CAGR
- TABLE 33: World 15-Year Perspective for Magnetic by Geographic Region - Percentage Breakdown of Value Sales for USA, Canada, Japan, China, Europe, Asia-Pacific, Latin America, Middle East and Africa for Years 2015, 2025 & 2030
- TABLE 34: World Recent Past, Current & Future Analysis for Other Technologies by Geographic Region - USA, Canada, Japan, China, Europe, Asia-Pacific, Latin America, Middle East and Africa Markets - Independent Analysis of Annual Sales in US$ Thousand for Years 2024 through 2030 and % CAGR
- TABLE 35: World Historic Review for Other Technologies by Geographic Region - USA, Canada, Japan, China, Europe, Asia-Pacific, Latin America, Middle East and Africa Markets - Independent Analysis of Annual Sales in US$ Thousand for Years 2015 through 2023 and % CAGR
- TABLE 36: World 15-Year Perspective for Other Technologies by Geographic Region - Percentage Breakdown of Value Sales for USA, Canada, Japan, China, Europe, Asia-Pacific, Latin America, Middle East and Africa for Years 2015, 2025 & 2030
- TABLE 37: World Encoders Market Analysis of Annual Sales in US$ Thousand for Years 2015 through 2030
- III. MARKET ANALYSIS
- UNITED STATES
- Encoders Market Presence - Strong/Active/Niche/Trivial - Key Competitors in the United States for 2025 (E)
- TABLE 38: USA Recent Past, Current & Future Analysis for Encoders by Type - Rotary and Linear - Independent Analysis of Annual Sales in US$ Thousand for the Years 2024 through 2030 and % CAGR
- TABLE 39: USA Historic Review for Encoders by Type - Rotary and Linear Markets - Independent Analysis of Annual Sales in US$ Thousand for Years 2015 through 2023 and % CAGR
- TABLE 40: USA 15-Year Perspective for Encoders by Type - Percentage Breakdown of Value Sales for Rotary and Linear for the Years 2015, 2025 & 2030
- TABLE 41: USA Recent Past, Current & Future Analysis for Encoders by End-Use - Medical, Other End-Uses, Industrial, Automotive, Consumer Electronics and Food & Beverage - Independent Analysis of Annual Sales in US$ Thousand for the Years 2024 through 2030 and % CAGR
- TABLE 42: USA Historic Review for Encoders by End-Use - Medical, Other End-Uses, Industrial, Automotive, Consumer Electronics and Food & Beverage Markets - Independent Analysis of Annual Sales in US$ Thousand for Years 2015 through 2023 and % CAGR
- TABLE 43: USA 15-Year Perspective for Encoders by End-Use - Percentage Breakdown of Value Sales for Medical, Other End-Uses, Industrial, Automotive, Consumer Electronics and Food & Beverage for the Years 2015, 2025 & 2030
- TABLE 44: USA Recent Past, Current & Future Analysis for Encoders by Technology - Optical, Magnetic and Other Technologies - Independent Analysis of Annual Sales in US$ Thousand for the Years 2024 through 2030 and % CAGR
- TABLE 45: USA Historic Review for Encoders by Technology - Optical, Magnetic and Other Technologies Markets - Independent Analysis of Annual Sales in US$ Thousand for Years 2015 through 2023 and % CAGR
- TABLE 46: USA 15-Year Perspective for Encoders by Technology - Percentage Breakdown of Value Sales for Optical, Magnetic and Other Technologies for the Years 2015, 2025 & 2030
- CANADA
- TABLE 47: Canada Recent Past, Current & Future Analysis for Encoders by Type - Rotary and Linear - Independent Analysis of Annual Sales in US$ Thousand for the Years 2024 through 2030 and % CAGR
- TABLE 48: Canada Historic Review for Encoders by Type - Rotary and Linear Markets - Independent Analysis of Annual Sales in US$ Thousand for Years 2015 through 2023 and % CAGR
- TABLE 49: Canada 15-Year Perspective for Encoders by Type - Percentage Breakdown of Value Sales for Rotary and Linear for the Years 2015, 2025 & 2030
- TABLE 50: Canada Recent Past, Current & Future Analysis for Encoders by End-Use - Medical, Other End-Uses, Industrial, Automotive, Consumer Electronics and Food & Beverage - Independent Analysis of Annual Sales in US$ Thousand for the Years 2024 through 2030 and % CAGR
- TABLE 51: Canada Historic Review for Encoders by End-Use - Medical, Other End-Uses, Industrial, Automotive, Consumer Electronics and Food & Beverage Markets - Independent Analysis of Annual Sales in US$ Thousand for Years 2015 through 2023 and % CAGR
- TABLE 52: Canada 15-Year Perspective for Encoders by End-Use - Percentage Breakdown of Value Sales for Medical, Other End-Uses, Industrial, Automotive, Consumer Electronics and Food & Beverage for the Years 2015, 2025 & 2030
- TABLE 53: Canada Recent Past, Current & Future Analysis for Encoders by Technology - Optical, Magnetic and Other Technologies - Independent Analysis of Annual Sales in US$ Thousand for the Years 2024 through 2030 and % CAGR
- TABLE 54: Canada Historic Review for Encoders by Technology - Optical, Magnetic and Other Technologies Markets - Independent Analysis of Annual Sales in US$ Thousand for Years 2015 through 2023 and % CAGR
- TABLE 55: Canada 15-Year Perspective for Encoders by Technology - Percentage Breakdown of Value Sales for Optical, Magnetic and Other Technologies for the Years 2015, 2025 & 2030
- JAPAN
- Encoders Market Presence - Strong/Active/Niche/Trivial - Key Competitors in Japan for 2025 (E)
- TABLE 56: Japan Recent Past, Current & Future Analysis for Encoders by Type - Rotary and Linear - Independent Analysis of Annual Sales in US$ Thousand for the Years 2024 through 2030 and % CAGR
- TABLE 57: Japan Historic Review for Encoders by Type - Rotary and Linear Markets - Independent Analysis of Annual Sales in US$ Thousand for Years 2015 through 2023 and % CAGR
- TABLE 58: Japan 15-Year Perspective for Encoders by Type - Percentage Breakdown of Value Sales for Rotary and Linear for the Years 2015, 2025 & 2030
- TABLE 59: Japan Recent Past, Current & Future Analysis for Encoders by End-Use - Medical, Other End-Uses, Industrial, Automotive, Consumer Electronics and Food & Beverage - Independent Analysis of Annual Sales in US$ Thousand for the Years 2024 through 2030 and % CAGR
- TABLE 60: Japan Historic Review for Encoders by End-Use - Medical, Other End-Uses, Industrial, Automotive, Consumer Electronics and Food & Beverage Markets - Independent Analysis of Annual Sales in US$ Thousand for Years 2015 through 2023 and % CAGR
- TABLE 61: Japan 15-Year Perspective for Encoders by End-Use - Percentage Breakdown of Value Sales for Medical, Other End-Uses, Industrial, Automotive, Consumer Electronics and Food & Beverage for the Years 2015, 2025 & 2030
- TABLE 62: Japan Recent Past, Current & Future Analysis for Encoders by Technology - Optical, Magnetic and Other Technologies - Independent Analysis of Annual Sales in US$ Thousand for the Years 2024 through 2030 and % CAGR
- TABLE 63: Japan Historic Review for Encoders by Technology - Optical, Magnetic and Other Technologies Markets - Independent Analysis of Annual Sales in US$ Thousand for Years 2015 through 2023 and % CAGR
- TABLE 64: Japan 15-Year Perspective for Encoders by Technology - Percentage Breakdown of Value Sales for Optical, Magnetic and Other Technologies for the Years 2015, 2025 & 2030
- CHINA
- Encoders Market Presence - Strong/Active/Niche/Trivial - Key Competitors in China for 2025 (E)
- TABLE 65: China Recent Past, Current & Future Analysis for Encoders by Type - Rotary and Linear - Independent Analysis of Annual Sales in US$ Thousand for the Years 2024 through 2030 and % CAGR
- TABLE 66: China Historic Review for Encoders by Type - Rotary and Linear Markets - Independent Analysis of Annual Sales in US$ Thousand for Years 2015 through 2023 and % CAGR
- TABLE 67: China 15-Year Perspective for Encoders by Type - Percentage Breakdown of Value Sales for Rotary and Linear for the Years 2015, 2025 & 2030
- TABLE 68: China Recent Past, Current & Future Analysis for Encoders by End-Use - Medical, Other End-Uses, Industrial, Automotive, Consumer Electronics and Food & Beverage - Independent Analysis of Annual Sales in US$ Thousand for the Years 2024 through 2030 and % CAGR
- TABLE 69: China Historic Review for Encoders by End-Use - Medical, Other End-Uses, Industrial, Automotive, Consumer Electronics and Food & Beverage Markets - Independent Analysis of Annual Sales in US$ Thousand for Years 2015 through 2023 and % CAGR
- TABLE 70: China 15-Year Perspective for Encoders by End-Use - Percentage Breakdown of Value Sales for Medical, Other End-Uses, Industrial, Automotive, Consumer Electronics and Food & Beverage for the Years 2015, 2025 & 2030
- TABLE 71: China Recent Past, Current & Future Analysis for Encoders by Technology - Optical, Magnetic and Other Technologies - Independent Analysis of Annual Sales in US$ Thousand for the Years 2024 through 2030 and % CAGR
- TABLE 72: China Historic Review for Encoders by Technology - Optical, Magnetic and Other Technologies Markets - Independent Analysis of Annual Sales in US$ Thousand for Years 2015 through 2023 and % CAGR
- TABLE 73: China 15-Year Perspective for Encoders by Technology - Percentage Breakdown of Value Sales for Optical, Magnetic and Other Technologies for the Years 2015, 2025 & 2030
- EUROPE
- Encoders Market Presence - Strong/Active/Niche/Trivial - Key Competitors in Europe for 2025 (E)
- TABLE 74: Europe Recent Past, Current & Future Analysis for Encoders by Geographic Region - France, Germany, Italy, UK, Spain, Russia and Rest of Europe Markets - Independent Analysis of Annual Sales in US$ Thousand for Years 2024 through 2030 and % CAGR
- TABLE 75: Europe Historic Review for Encoders by Geographic Region - France, Germany, Italy, UK, Spain, Russia and Rest of Europe Markets - Independent Analysis of Annual Sales in US$ Thousand for Years 2015 through 2023 and % CAGR
- TABLE 76: Europe 15-Year Perspective for Encoders by Geographic Region - Percentage Breakdown of Value Sales for France, Germany, Italy, UK, Spain, Russia and Rest of Europe Markets for Years 2015, 2025 & 2030
- TABLE 77: Europe Recent Past, Current & Future Analysis for Encoders by Type - Rotary and Linear - Independent Analysis of Annual Sales in US$ Thousand for the Years 2024 through 2030 and % CAGR
- TABLE 78: Europe Historic Review for Encoders by Type - Rotary and Linear Markets - Independent Analysis of Annual Sales in US$ Thousand for Years 2015 through 2023 and % CAGR
- TABLE 79: Europe 15-Year Perspective for Encoders by Type - Percentage Breakdown of Value Sales for Rotary and Linear for the Years 2015, 2025 & 2030
- TABLE 80: Europe Recent Past, Current & Future Analysis for Encoders by End-Use - Medical, Other End-Uses, Industrial, Automotive, Consumer Electronics and Food & Beverage - Independent Analysis of Annual Sales in US$ Thousand for the Years 2024 through 2030 and % CAGR
- TABLE 81: Europe Historic Review for Encoders by End-Use - Medical, Other End-Uses, Industrial, Automotive, Consumer Electronics and Food & Beverage Markets - Independent Analysis of Annual Sales in US$ Thousand for Years 2015 through 2023 and % CAGR
- TABLE 82: Europe 15-Year Perspective for Encoders by End-Use - Percentage Breakdown of Value Sales for Medical, Other End-Uses, Industrial, Automotive, Consumer Electronics and Food & Beverage for the Years 2015, 2025 & 2030
- TABLE 83: Europe Recent Past, Current & Future Analysis for Encoders by Technology - Optical, Magnetic and Other Technologies - Independent Analysis of Annual Sales in US$ Thousand for the Years 2024 through 2030 and % CAGR
- TABLE 84: Europe Historic Review for Encoders by Technology - Optical, Magnetic and Other Technologies Markets - Independent Analysis of Annual Sales in US$ Thousand for Years 2015 through 2023 and % CAGR
- TABLE 85: Europe 15-Year Perspective for Encoders by Technology - Percentage Breakdown of Value Sales for Optical, Magnetic and Other Technologies for the Years 2015, 2025 & 2030
- FRANCE
- Encoders Market Presence - Strong/Active/Niche/Trivial - Key Competitors in France for 2025 (E)
- TABLE 86: France Recent Past, Current & Future Analysis for Encoders by Type - Rotary and Linear - Independent Analysis of Annual Sales in US$ Thousand for the Years 2024 through 2030 and % CAGR
- TABLE 87: France Historic Review for Encoders by Type - Rotary and Linear Markets - Independent Analysis of Annual Sales in US$ Thousand for Years 2015 through 2023 and % CAGR
- TABLE 88: France 15-Year Perspective for Encoders by Type - Percentage Breakdown of Value Sales for Rotary and Linear for the Years 2015, 2025 & 2030
- TABLE 89: France Recent Past, Current & Future Analysis for Encoders by End-Use - Medical, Other End-Uses, Industrial, Automotive, Consumer Electronics and Food & Beverage - Independent Analysis of Annual Sales in US$ Thousand for the Years 2024 through 2030 and % CAGR
- TABLE 90: France Historic Review for Encoders by End-Use - Medical, Other End-Uses, Industrial, Automotive, Consumer Electronics and Food & Beverage Markets - Independent Analysis of Annual Sales in US$ Thousand for Years 2015 through 2023 and % CAGR
- TABLE 91: France 15-Year Perspective for Encoders by End-Use - Percentage Breakdown of Value Sales for Medical, Other End-Uses, Industrial, Automotive, Consumer Electronics and Food & Beverage for the Years 2015, 2025 & 2030
- TABLE 92: France Recent Past, Current & Future Analysis for Encoders by Technology - Optical, Magnetic and Other Technologies - Independent Analysis of Annual Sales in US$ Thousand for the Years 2024 through 2030 and % CAGR
- TABLE 93: France Historic Review for Encoders by Technology - Optical, Magnetic and Other Technologies Markets - Independent Analysis of Annual Sales in US$ Thousand for Years 2015 through 2023 and % CAGR
- TABLE 94: France 15-Year Perspective for Encoders by Technology - Percentage Breakdown of Value Sales for Optical, Magnetic and Other Technologies for the Years 2015, 2025 & 2030
- GERMANY
- Encoders Market Presence - Strong/Active/Niche/Trivial - Key Competitors in Germany for 2025 (E)
- TABLE 95: Germany Recent Past, Current & Future Analysis for Encoders by Type - Rotary and Linear - Independent Analysis of Annual Sales in US$ Thousand for the Years 2024 through 2030 and % CAGR
- TABLE 96: Germany Historic Review for Encoders by Type - Rotary and Linear Markets - Independent Analysis of Annual Sales in US$ Thousand for Years 2015 through 2023 and % CAGR
- TABLE 97: Germany 15-Year Perspective for Encoders by Type - Percentage Breakdown of Value Sales for Rotary and Linear for the Years 2015, 2025 & 2030
- TABLE 98: Germany Recent Past, Current & Future Analysis for Encoders by End-Use - Medical, Other End-Uses, Industrial, Automotive, Consumer Electronics and Food & Beverage - Independent Analysis of Annual Sales in US$ Thousand for the Years 2024 through 2030 and % CAGR
- TABLE 99: Germany Historic Review for Encoders by End-Use - Medical, Other End-Uses, Industrial, Automotive, Consumer Electronics and Food & Beverage Markets - Independent Analysis of Annual Sales in US$ Thousand for Years 2015 through 2023 and % CAGR
- TABLE 100: Germany 15-Year Perspective for Encoders by End-Use - Percentage Breakdown of Value Sales for Medical, Other End-Uses, Industrial, Automotive, Consumer Electronics and Food & Beverage for the Years 2015, 2025 & 2030
- TABLE 101: Germany Recent Past, Current & Future Analysis for Encoders by Technology - Optical, Magnetic and Other Technologies - Independent Analysis of Annual Sales in US$ Thousand for the Years 2024 through 2030 and % CAGR
- TABLE 102: Germany Historic Review for Encoders by Technology - Optical, Magnetic and Other Technologies Markets - Independent Analysis of Annual Sales in US$ Thousand for Years 2015 through 2023 and % CAGR
- TABLE 103: Germany 15-Year Perspective for Encoders by Technology - Percentage Breakdown of Value Sales for Optical, Magnetic and Other Technologies for the Years 2015, 2025 & 2030
- ITALY
- TABLE 104: Italy Recent Past, Current & Future Analysis for Encoders by Type - Rotary and Linear - Independent Analysis of Annual Sales in US$ Thousand for the Years 2024 through 2030 and % CAGR
- TABLE 105: Italy Historic Review for Encoders by Type - Rotary and Linear Markets - Independent Analysis of Annual Sales in US$ Thousand for Years 2015 through 2023 and % CAGR
- TABLE 106: Italy 15-Year Perspective for Encoders by Type - Percentage Breakdown of Value Sales for Rotary and Linear for the Years 2015, 2025 & 2030
- TABLE 107: Italy Recent Past, Current & Future Analysis for Encoders by End-Use - Medical, Other End-Uses, Industrial, Automotive, Consumer Electronics and Food & Beverage - Independent Analysis of Annual Sales in US$ Thousand for the Years 2024 through 2030 and % CAGR
- TABLE 108: Italy Historic Review for Encoders by End-Use - Medical, Other End-Uses, Industrial, Automotive, Consumer Electronics and Food & Beverage Markets - Independent Analysis of Annual Sales in US$ Thousand for Years 2015 through 2023 and % CAGR
- TABLE 109: Italy 15-Year Perspective for Encoders by End-Use - Percentage Breakdown of Value Sales for Medical, Other End-Uses, Industrial, Automotive, Consumer Electronics and Food & Beverage for the Years 2015, 2025 & 2030
- TABLE 110: Italy Recent Past, Current & Future Analysis for Encoders by Technology - Optical, Magnetic and Other Technologies - Independent Analysis of Annual Sales in US$ Thousand for the Years 2024 through 2030 and % CAGR
- TABLE 111: Italy Historic Review for Encoders by Technology - Optical, Magnetic and Other Technologies Markets - Independent Analysis of Annual Sales in US$ Thousand for Years 2015 through 2023 and % CAGR
- TABLE 112: Italy 15-Year Perspective for Encoders by Technology - Percentage Breakdown of Value Sales for Optical, Magnetic and Other Technologies for the Years 2015, 2025 & 2030
- UNITED KINGDOM
- Encoders Market Presence - Strong/Active/Niche/Trivial - Key Competitors in the United Kingdom for 2025 (E)
- TABLE 113: UK Recent Past, Current & Future Analysis for Encoders by Type - Rotary and Linear - Independent Analysis of Annual Sales in US$ Thousand for the Years 2024 through 2030 and % CAGR
- TABLE 114: UK Historic Review for Encoders by Type - Rotary and Linear Markets - Independent Analysis of Annual Sales in US$ Thousand for Years 2015 through 2023 and % CAGR
- TABLE 115: UK 15-Year Perspective for Encoders by Type - Percentage Breakdown of Value Sales for Rotary and Linear for the Years 2015, 2025 & 2030
- TABLE 116: UK Recent Past, Current & Future Analysis for Encoders by End-Use - Medical, Other End-Uses, Industrial, Automotive, Consumer Electronics and Food & Beverage - Independent Analysis of Annual Sales in US$ Thousand for the Years 2024 through 2030 and % CAGR
- TABLE 117: UK Historic Review for Encoders by End-Use - Medical, Other End-Uses, Industrial, Automotive, Consumer Electronics and Food & Beverage Markets - Independent Analysis of Annual Sales in US$ Thousand for Years 2015 through 2023 and % CAGR
- TABLE 118: UK 15-Year Perspective for Encoders by End-Use - Percentage Breakdown of Value Sales for Medical, Other End-Uses, Industrial, Automotive, Consumer Electronics and Food & Beverage for the Years 2015, 2025 & 2030
- TABLE 119: UK Recent Past, Current & Future Analysis for Encoders by Technology - Optical, Magnetic and Other Technologies - Independent Analysis of Annual Sales in US$ Thousand for the Years 2024 through 2030 and % CAGR
- TABLE 120: UK Historic Review for Encoders by Technology - Optical, Magnetic and Other Technologies Markets - Independent Analysis of Annual Sales in US$ Thousand for Years 2015 through 2023 and % CAGR
- TABLE 121: UK 15-Year Perspective for Encoders by Technology - Percentage Breakdown of Value Sales for Optical, Magnetic and Other Technologies for the Years 2015, 2025 & 2030
- SPAIN
- TABLE 122: Spain Recent Past, Current & Future Analysis for Encoders by Type - Rotary and Linear - Independent Analysis of Annual Sales in US$ Thousand for the Years 2024 through 2030 and % CAGR
- TABLE 123: Spain Historic Review for Encoders by Type - Rotary and Linear Markets - Independent Analysis of Annual Sales in US$ Thousand for Years 2015 through 2023 and % CAGR
- TABLE 124: Spain 15-Year Perspective for Encoders by Type - Percentage Breakdown of Value Sales for Rotary and Linear for the Years 2015, 2025 & 2030
- TABLE 125: Spain Recent Past, Current & Future Analysis for Encoders by End-Use - Medical, Other End-Uses, Industrial, Automotive, Consumer Electronics and Food & Beverage - Independent Analysis of Annual Sales in US$ Thousand for the Years 2024 through 2030 and % CAGR
- TABLE 126: Spain Historic Review for Encoders by End-Use - Medical, Other End-Uses, Industrial, Automotive, Consumer Electronics and Food & Beverage Markets - Independent Analysis of Annual Sales in US$ Thousand for Years 2015 through 2023 and % CAGR
- TABLE 127: Spain 15-Year Perspective for Encoders by End-Use - Percentage Breakdown of Value Sales for Medical, Other End-Uses, Industrial, Automotive, Consumer Electronics and Food & Beverage for the Years 2015, 2025 & 2030
- TABLE 128: Spain Recent Past, Current & Future Analysis for Encoders by Technology - Optical, Magnetic and Other Technologies - Independent Analysis of Annual Sales in US$ Thousand for the Years 2024 through 2030 and % CAGR
- TABLE 129: Spain Historic Review for Encoders by Technology - Optical, Magnetic and Other Technologies Markets - Independent Analysis of Annual Sales in US$ Thousand for Years 2015 through 2023 and % CAGR
- TABLE 130: Spain 15-Year Perspective for Encoders by Technology - Percentage Breakdown of Value Sales for Optical, Magnetic and Other Technologies for the Years 2015, 2025 & 2030
- RUSSIA
- TABLE 131: Russia Recent Past, Current & Future Analysis for Encoders by Type - Rotary and Linear - Independent Analysis of Annual Sales in US$ Thousand for the Years 2024 through 2030 and % CAGR
- TABLE 132: Russia Historic Review for Encoders by Type - Rotary and Linear Markets - Independent Analysis of Annual Sales in US$ Thousand for Years 2015 through 2023 and % CAGR
- TABLE 133: Russia 15-Year Perspective for Encoders by Type - Percentage Breakdown of Value Sales for Rotary and Linear for the Years 2015, 2025 & 2030
- TABLE 134: Russia Recent Past, Current & Future Analysis for Encoders by End-Use - Medical, Other End-Uses, Industrial, Automotive, Consumer Electronics and Food & Beverage - Independent Analysis of Annual Sales in US$ Thousand for the Years 2024 through 2030 and % CAGR
- TABLE 135: Russia Historic Review for Encoders by End-Use - Medical, Other End-Uses, Industrial, Automotive, Consumer Electronics and Food & Beverage Markets - Independent Analysis of Annual Sales in US$ Thousand for Years 2015 through 2023 and % CAGR
- TABLE 136: Russia 15-Year Perspective for Encoders by End-Use - Percentage Breakdown of Value Sales for Medical, Other End-Uses, Industrial, Automotive, Consumer Electronics and Food & Beverage for the Years 2015, 2025 & 2030
- TABLE 137: Russia Recent Past, Current & Future Analysis for Encoders by Technology - Optical, Magnetic and Other Technologies - Independent Analysis of Annual Sales in US$ Thousand for the Years 2024 through 2030 and % CAGR
- TABLE 138: Russia Historic Review for Encoders by Technology - Optical, Magnetic and Other Technologies Markets - Independent Analysis of Annual Sales in US$ Thousand for Years 2015 through 2023 and % CAGR
- TABLE 139: Russia 15-Year Perspective for Encoders by Technology - Percentage Breakdown of Value Sales for Optical, Magnetic and Other Technologies for the Years 2015, 2025 & 2030
- REST OF EUROPE
- TABLE 140: Rest of Europe Recent Past, Current & Future Analysis for Encoders by Type - Rotary and Linear - Independent Analysis of Annual Sales in US$ Thousand for the Years 2024 through 2030 and % CAGR
- TABLE 141: Rest of Europe Historic Review for Encoders by Type - Rotary and Linear Markets - Independent Analysis of Annual Sales in US$ Thousand for Years 2015 through 2023 and % CAGR
- TABLE 142: Rest of Europe 15-Year Perspective for Encoders by Type - Percentage Breakdown of Value Sales for Rotary and Linear for the Years 2015, 2025 & 2030
- TABLE 143: Rest of Europe Recent Past, Current & Future Analysis for Encoders by End-Use - Medical, Other End-Uses, Industrial, Automotive, Consumer Electronics and Food & Beverage - Independent Analysis of Annual Sales in US$ Thousand for the Years 2024 through 2030 and % CAGR
- TABLE 144: Rest of Europe Historic Review for Encoders by End-Use - Medical, Other End-Uses, Industrial, Automotive, Consumer Electronics and Food & Beverage Markets - Independent Analysis of Annual Sales in US$ Thousand for Years 2015 through 2023 and % CAGR
- TABLE 145: Rest of Europe 15-Year Perspective for Encoders by End-Use - Percentage Breakdown of Value Sales for Medical, Other End-Uses, Industrial, Automotive, Consumer Electronics and Food & Beverage for the Years 2015, 2025 & 2030
- TABLE 146: Rest of Europe Recent Past, Current & Future Analysis for Encoders by Technology - Optical, Magnetic and Other Technologies - Independent Analysis of Annual Sales in US$ Thousand for the Years 2024 through 2030 and % CAGR
- TABLE 147: Rest of Europe Historic Review for Encoders by Technology - Optical, Magnetic and Other Technologies Markets - Independent Analysis of Annual Sales in US$ Thousand for Years 2015 through 2023 and % CAGR
- TABLE 148: Rest of Europe 15-Year Perspective for Encoders by Technology - Percentage Breakdown of Value Sales for Optical, Magnetic and Other Technologies for the Years 2015, 2025 & 2030
- ASIA-PACIFIC
- Encoders Market Presence - Strong/Active/Niche/Trivial - Key Competitors in Asia-Pacific for 2025 (E)
- TABLE 149: Asia-Pacific Recent Past, Current & Future Analysis for Encoders by Geographic Region - Australia, India, South Korea and Rest of Asia-Pacific Markets - Independent Analysis of Annual Sales in US$ Thousand for Years 2024 through 2030 and % CAGR
- TABLE 150: Asia-Pacific Historic Review for Encoders by Geographic Region - Australia, India, South Korea and Rest of Asia-Pacific Markets - Independent Analysis of Annual Sales in US$ Thousand for Years 2015 through 2023 and % CAGR
- TABLE 151: Asia-Pacific 15-Year Perspective for Encoders by Geographic Region - Percentage Breakdown of Value Sales for Australia, India, South Korea and Rest of Asia-Pacific Markets for Years 2015, 2025 & 2030
- TABLE 152: Asia-Pacific Recent Past, Current & Future Analysis for Encoders by Type - Rotary and Linear - Independent Analysis of Annual Sales in US$ Thousand for the Years 2024 through 2030 and % CAGR
- TABLE 153: Asia-Pacific Historic Review for Encoders by Type - Rotary and Linear Markets - Independent Analysis of Annual Sales in US$ Thousand for Years 2015 through 2023 and % CAGR
- TABLE 154: Asia-Pacific 15-Year Perspective for Encoders by Type - Percentage Breakdown of Value Sales for Rotary and Linear for the Years 2015, 2025 & 2030
- TABLE 155: Asia-Pacific Recent Past, Current & Future Analysis for Encoders by End-Use - Medical, Other End-Uses, Industrial, Automotive, Consumer Electronics and Food & Beverage - Independent Analysis of Annual Sales in US$ Thousand for the Years 2024 through 2030 and % CAGR
- TABLE 156: Asia-Pacific Historic Review for Encoders by End-Use - Medical, Other End-Uses, Industrial, Automotive, Consumer Electronics and Food & Beverage Markets - Independent Analysis of Annual Sales in US$ Thousand for Years 2015 through 2023 and % CAGR
- TABLE 157: Asia-Pacific 15-Year Perspective for Encoders by End-Use - Percentage Breakdown of Value Sales for Medical, Other End-Uses, Industrial, Automotive, Consumer Electronics and Food & Beverage for the Years 2015, 2025 & 2030
- TABLE 158: Asia-Pacific Recent Past, Current & Future Analysis for Encoders by Technology - Optical, Magnetic and Other Technologies - Independent Analysis of Annual Sales in US$ Thousand for the Years 2024 through 2030 and % CAGR
- TABLE 159: Asia-Pacific Historic Review for Encoders by Technology - Optical, Magnetic and Other Technologies Markets - Independent Analysis of Annual Sales in US$ Thousand for Years 2015 through 2023 and % CAGR
- TABLE 160: Asia-Pacific 15-Year Perspective for Encoders by Technology - Percentage Breakdown of Value Sales for Optical, Magnetic and Other Technologies for the Years 2015, 2025 & 2030
- AUSTRALIA
- Encoders Market Presence - Strong/Active/Niche/Trivial - Key Competitors in Australia for 2025 (E)
- TABLE 161: Australia Recent Past, Current & Future Analysis for Encoders by Type - Rotary and Linear - Independent Analysis of Annual Sales in US$ Thousand for the Years 2024 through 2030 and % CAGR
- TABLE 162: Australia Historic Review for Encoders by Type - Rotary and Linear Markets - Independent Analysis of Annual Sales in US$ Thousand for Years 2015 through 2023 and % CAGR
- TABLE 163: Australia 15-Year Perspective for Encoders by Type - Percentage Breakdown of Value Sales for Rotary and Linear for the Years 2015, 2025 & 2030
- TABLE 164: Australia Recent Past, Current & Future Analysis for Encoders by End-Use - Medical, Other End-Uses, Industrial, Automotive, Consumer Electronics and Food & Beverage - Independent Analysis of Annual Sales in US$ Thousand for the Years 2024 through 2030 and % CAGR
- TABLE 165: Australia Historic Review for Encoders by End-Use - Medical, Other End-Uses, Industrial, Automotive, Consumer Electronics and Food & Beverage Markets - Independent Analysis of Annual Sales in US$ Thousand for Years 2015 through 2023 and % CAGR
- TABLE 166: Australia 15-Year Perspective for Encoders by End-Use - Percentage Breakdown of Value Sales for Medical, Other End-Uses, Industrial, Automotive, Consumer Electronics and Food & Beverage for the Years 2015, 2025 & 2030
- TABLE 167: Australia Recent Past, Current & Future Analysis for Encoders by Technology - Optical, Magnetic and Other Technologies - Independent Analysis of Annual Sales in US$ Thousand for the Years 2024 through 2030 and % CAGR
- TABLE 168: Australia Historic Review for Encoders by Technology - Optical, Magnetic and Other Technologies Markets - Independent Analysis of Annual Sales in US$ Thousand for Years 2015 through 2023 and % CAGR
- TABLE 169: Australia 15-Year Perspective for Encoders by Technology - Percentage Breakdown of Value Sales for Optical, Magnetic and Other Technologies for the Years 2015, 2025 & 2030
- INDIA
- Encoders Market Presence - Strong/Active/Niche/Trivial - Key Competitors in India for 2025 (E)
- TABLE 170: India Recent Past, Current & Future Analysis for Encoders by Type - Rotary and Linear - Independent Analysis of Annual Sales in US$ Thousand for the Years 2024 through 2030 and % CAGR
- TABLE 171: India Historic Review for Encoders by Type - Rotary and Linear Markets - Independent Analysis of Annual Sales in US$ Thousand for Years 2015 through 2023 and % CAGR
- TABLE 172: India 15-Year Perspective for Encoders by Type - Percentage Breakdown of Value Sales for Rotary and Linear for the Years 2015, 2025 & 2030
- TABLE 173: India Recent Past, Current & Future Analysis for Encoders by End-Use - Medical, Other End-Uses, Industrial, Automotive, Consumer Electronics and Food & Beverage - Independent Analysis of Annual Sales in US$ Thousand for the Years 2024 through 2030 and % CAGR
- TABLE 174: India Historic Review for Encoders by End-Use - Medical, Other End-Uses, Industrial, Automotive, Consumer Electronics and Food & Beverage Markets - Independent Analysis of Annual Sales in US$ Thousand for Years 2015 through 2023 and % CAGR
- TABLE 175: India 15-Year Perspective for Encoders by End-Use - Percentage Breakdown of Value Sales for Medical, Other End-Uses, Industrial, Automotive, Consumer Electronics and Food & Beverage for the Years 2015, 2025 & 2030
- TABLE 176: India Recent Past, Current & Future Analysis for Encoders by Technology - Optical, Magnetic and Other Technologies - Independent Analysis of Annual Sales in US$ Thousand for the Years 2024 through 2030 and % CAGR
- TABLE 177: India Historic Review for Encoders by Technology - Optical, Magnetic and Other Technologies Markets - Independent Analysis of Annual Sales in US$ Thousand for Years 2015 through 2023 and % CAGR
- TABLE 178: India 15-Year Perspective for Encoders by Technology - Percentage Breakdown of Value Sales for Optical, Magnetic and Other Technologies for the Years 2015, 2025 & 2030
- SOUTH KOREA
- TABLE 179: South Korea Recent Past, Current & Future Analysis for Encoders by Type - Rotary and Linear - Independent Analysis of Annual Sales in US$ Thousand for the Years 2024 through 2030 and % CAGR
- TABLE 180: South Korea Historic Review for Encoders by Type - Rotary and Linear Markets - Independent Analysis of Annual Sales in US$ Thousand for Years 2015 through 2023 and % CAGR
- TABLE 181: South Korea 15-Year Perspective for Encoders by Type - Percentage Breakdown of Value Sales for Rotary and Linear for the Years 2015, 2025 & 2030
- TABLE 182: South Korea Recent Past, Current & Future Analysis for Encoders by End-Use - Medical, Other End-Uses, Industrial, Automotive, Consumer Electronics and Food & Beverage - Independent Analysis of Annual Sales in US$ Thousand for the Years 2024 through 2030 and % CAGR
- TABLE 183: South Korea Historic Review for Encoders by End-Use - Medical, Other End-Uses, Industrial, Automotive, Consumer Electronics and Food & Beverage Markets - Independent Analysis of Annual Sales in US$ Thousand for Years 2015 through 2023 and % CAGR
- TABLE 184: South Korea 15-Year Perspective for Encoders by End-Use - Percentage Breakdown of Value Sales for Medical, Other End-Uses, Industrial, Automotive, Consumer Electronics and Food & Beverage for the Years 2015, 2025 & 2030
- TABLE 185: South Korea Recent Past, Current & Future Analysis for Encoders by Technology - Optical, Magnetic and Other Technologies - Independent Analysis of Annual Sales in US$ Thousand for the Years 2024 through 2030 and % CAGR
- TABLE 186: South Korea Historic Review for Encoders by Technology - Optical, Magnetic and Other Technologies Markets - Independent Analysis of Annual Sales in US$ Thousand for Years 2015 through 2023 and % CAGR
- TABLE 187: South Korea 15-Year Perspective for Encoders by Technology - Percentage Breakdown of Value Sales for Optical, Magnetic and Other Technologies for the Years 2015, 2025 & 2030
- REST OF ASIA-PACIFIC
- TABLE 188: Rest of Asia-Pacific Recent Past, Current & Future Analysis for Encoders by Type - Rotary and Linear - Independent Analysis of Annual Sales in US$ Thousand for the Years 2024 through 2030 and % CAGR
- TABLE 189: Rest of Asia-Pacific Historic Review for Encoders by Type - Rotary and Linear Markets - Independent Analysis of Annual Sales in US$ Thousand for Years 2015 through 2023 and % CAGR
- TABLE 190: Rest of Asia-Pacific 15-Year Perspective for Encoders by Type - Percentage Breakdown of Value Sales for Rotary and Linear for the Years 2015, 2025 & 2030
- TABLE 191: Rest of Asia-Pacific Recent Past, Current & Future Analysis for Encoders by End-Use - Medical, Other End-Uses, Industrial, Automotive, Consumer Electronics and Food & Beverage - Independent Analysis of Annual Sales in US$ Thousand for the Years 2024 through 2030 and % CAGR
- TABLE 192: Rest of Asia-Pacific Historic Review for Encoders by End-Use - Medical, Other End-Uses, Industrial, Automotive, Consumer Electronics and Food & Beverage Markets - Independent Analysis of Annual Sales in US$ Thousand for Years 2015 through 2023 and % CAGR
- TABLE 193: Rest of Asia-Pacific 15-Year Perspective for Encoders by End-Use - Percentage Breakdown of Value Sales for Medical, Other End-Uses, Industrial, Automotive, Consumer Electronics and Food & Beverage for the Years 2015, 2025 & 2030
- TABLE 194: Rest of Asia-Pacific Recent Past, Current & Future Analysis for Encoders by Technology - Optical, Magnetic and Other Technologies - Independent Analysis of Annual Sales in US$ Thousand for the Years 2024 through 2030 and % CAGR
- TABLE 195: Rest of Asia-Pacific Historic Review for Encoders by Technology - Optical, Magnetic and Other Technologies Markets - Independent Analysis of Annual Sales in US$ Thousand for Years 2015 through 2023 and % CAGR
- TABLE 196: Rest of Asia-Pacific 15-Year Perspective for Encoders by Technology - Percentage Breakdown of Value Sales for Optical, Magnetic and Other Technologies for the Years 2015, 2025 & 2030
- LATIN AMERICA
- Encoders Market Presence - Strong/Active/Niche/Trivial - Key Competitors in Latin America for 2025 (E)
- TABLE 197: Latin America Recent Past, Current & Future Analysis for Encoders by Geographic Region - Argentina, Brazil, Mexico and Rest of Latin America Markets - Independent Analysis of Annual Sales in US$ Thousand for Years 2024 through 2030 and % CAGR
- TABLE 198: Latin America Historic Review for Encoders by Geographic Region - Argentina, Brazil, Mexico and Rest of Latin America Markets - Independent Analysis of Annual Sales in US$ Thousand for Years 2015 through 2023 and % CAGR
- TABLE 199: Latin America 15-Year Perspective for Encoders by Geographic Region - Percentage Breakdown of Value Sales for Argentina, Brazil, Mexico and Rest of Latin America Markets for Years 2015, 2025 & 2030
- TABLE 200: Latin America Recent Past, Current & Future Analysis for Encoders by Type - Rotary and Linear - Independent Analysis of Annual Sales in US$ Thousand for the Years 2024 through 2030 and % CAGR
- TABLE 201: Latin America Historic Review for Encoders by Type - Rotary and Linear Markets - Independent Analysis of Annual Sales in US$ Thousand for Years 2015 through 2023 and % CAGR
- TABLE 202: Latin America 15-Year Perspective for Encoders by Type - Percentage Breakdown of Value Sales for Rotary and Linear for the Years 2015, 2025 & 2030
- TABLE 203: Latin America Recent Past, Current & Future Analysis for Encoders by End-Use - Medical, Other End-Uses, Industrial, Automotive, Consumer Electronics and Food & Beverage - Independent Analysis of Annual Sales in US$ Thousand for the Years 2024 through 2030 and % CAGR
- TABLE 204: Latin America Historic Review for Encoders by End-Use - Medical, Other End-Uses, Industrial, Automotive, Consumer Electronics and Food & Beverage Markets - Independent Analysis of Annual Sales in US$ Thousand for Years 2015 through 2023 and % CAGR
- TABLE 205: Latin America 15-Year Perspective for Encoders by End-Use - Percentage Breakdown of Value Sales for Medical, Other End-Uses, Industrial, Automotive, Consumer Electronics and Food & Beverage for the Years 2015, 2025 & 2030
- TABLE 206: Latin America Recent Past, Current & Future Analysis for Encoders by Technology - Optical, Magnetic and Other Technologies - Independent Analysis of Annual Sales in US$ Thousand for the Years 2024 through 2030 and % CAGR
- TABLE 207: Latin America Historic Review for Encoders by Technology - Optical, Magnetic and Other Technologies Markets - Independent Analysis of Annual Sales in US$ Thousand for Years 2015 through 2023 and % CAGR
- TABLE 208: Latin America 15-Year Perspective for Encoders by Technology - Percentage Breakdown of Value Sales for Optical, Magnetic and Other Technologies for the Years 2015, 2025 & 2030
- ARGENTINA
- TABLE 209: Argentina Recent Past, Current & Future Analysis for Encoders by Type - Rotary and Linear - Independent Analysis of Annual Sales in US$ Thousand for the Years 2024 through 2030 and % CAGR
- TABLE 210: Argentina Historic Review for Encoders by Type - Rotary and Linear Markets - Independent Analysis of Annual Sales in US$ Thousand for Years 2015 through 2023 and % CAGR
- TABLE 211: Argentina 15-Year Perspective for Encoders by Type - Percentage Breakdown of Value Sales for Rotary and Linear for the Years 2015, 2025 & 2030
- TABLE 212: Argentina Recent Past, Current & Future Analysis for Encoders by End-Use - Medical, Other End-Uses, Industrial, Automotive, Consumer Electronics and Food & Beverage - Independent Analysis of Annual Sales in US$ Thousand for the Years 2024 through 2030 and % CAGR
- TABLE 213: Argentina Historic Review for Encoders by End-Use - Medical, Other End-Uses, Industrial, Automotive, Consumer Electronics and Food & Beverage Markets - Independent Analysis of Annual Sales in US$ Thousand for Years 2015 through 2023 and % CAGR
- TABLE 214: Argentina 15-Year Perspective for Encoders by End-Use - Percentage Breakdown of Value Sales for Medical, Other End-Uses, Industrial, Automotive, Consumer Electronics and Food & Beverage for the Years 2015, 2025 & 2030
- TABLE 215: Argentina Recent Past, Current & Future Analysis for Encoders by Technology - Optical, Magnetic and Other Technologies - Independent Analysis of Annual Sales in US$ Thousand for the Years 2024 through 2030 and % CAGR
- TABLE 216: Argentina Historic Review for Encoders by Technology - Optical, Magnetic and Other Technologies Markets - Independent Analysis of Annual Sales in US$ Thousand for Years 2015 through 2023 and % CAGR
- TABLE 217: Argentina 15-Year Perspective for Encoders by Technology - Percentage Breakdown of Value Sales for Optical, Magnetic and Other Technologies for the Years 2015, 2025 & 2030
- BRAZIL
- TABLE 218: Brazil Recent Past, Current & Future Analysis for Encoders by Type - Rotary and Linear - Independent Analysis of Annual Sales in US$ Thousand for the Years 2024 through 2030 and % CAGR
- TABLE 219: Brazil Historic Review for Encoders by Type - Rotary and Linear Markets - Independent Analysis of Annual Sales in US$ Thousand for Years 2015 through 2023 and % CAGR
- TABLE 220: Brazil 15-Year Perspective for Encoders by Type - Percentage Breakdown of Value Sales for Rotary and Linear for the Years 2015, 2025 & 2030
- TABLE 221: Brazil Recent Past, Current & Future Analysis for Encoders by End-Use - Medical, Other End-Uses, Industrial, Automotive, Consumer Electronics and Food & Beverage - Independent Analysis of Annual Sales in US$ Thousand for the Years 2024 through 2030 and % CAGR
- TABLE 222: Brazil Historic Review for Encoders by End-Use - Medical, Other End-Uses, Industrial, Automotive, Consumer Electronics and Food & Beverage Markets - Independent Analysis of Annual Sales in US$ Thousand for Years 2015 through 2023 and % CAGR
- TABLE 223: Brazil 15-Year Perspective for Encoders by End-Use - Percentage Breakdown of Value Sales for Medical, Other End-Uses, Industrial, Automotive, Consumer Electronics and Food & Beverage for the Years 2015, 2025 & 2030
- TABLE 224: Brazil Recent Past, Current & Future Analysis for Encoders by Technology - Optical, Magnetic and Other Technologies - Independent Analysis of Annual Sales in US$ Thousand for the Years 2024 through 2030 and % CAGR
- TABLE 225: Brazil Historic Review for Encoders by Technology - Optical, Magnetic and Other Technologies Markets - Independent Analysis of Annual Sales in US$ Thousand for Years 2015 through 2023 and % CAGR
- TABLE 226: Brazil 15-Year Perspective for Encoders by Technology - Percentage Breakdown of Value Sales for Optical, Magnetic and Other Technologies for the Years 2015, 2025 & 2030
- MEXICO
- TABLE 227: Mexico Recent Past, Current & Future Analysis for Encoders by Type - Rotary and Linear - Independent Analysis of Annual Sales in US$ Thousand for the Years 2024 through 2030 and % CAGR
- TABLE 228: Mexico Historic Review for Encoders by Type - Rotary and Linear Markets - Independent Analysis of Annual Sales in US$ Thousand for Years 2015 through 2023 and % CAGR
- TABLE 229: Mexico 15-Year Perspective for Encoders by Type - Percentage Breakdown of Value Sales for Rotary and Linear for the Years 2015, 2025 & 2030
- TABLE 230: Mexico Recent Past, Current & Future Analysis for Encoders by End-Use - Medical, Other End-Uses, Industrial, Automotive, Consumer Electronics and Food & Beverage - Independent Analysis of Annual Sales in US$ Thousand for the Years 2024 through 2030 and % CAGR
- TABLE 231: Mexico Historic Review for Encoders by End-Use - Medical, Other End-Uses, Industrial, Automotive, Consumer Electronics and Food & Beverage Markets - Independent Analysis of Annual Sales in US$ Thousand for Years 2015 through 2023 and % CAGR
- TABLE 232: Mexico 15-Year Perspective for Encoders by End-Use - Percentage Breakdown of Value Sales for Medical, Other End-Uses, Industrial, Automotive, Consumer Electronics and Food & Beverage for the Years 2015, 2025 & 2030
- TABLE 233: Mexico Recent Past, Current & Future Analysis for Encoders by Technology - Optical, Magnetic and Other Technologies - Independent Analysis of Annual Sales in US$ Thousand for the Years 2024 through 2030 and % CAGR
- TABLE 234: Mexico Historic Review for Encoders by Technology - Optical, Magnetic and Other Technologies Markets - Independent Analysis of Annual Sales in US$ Thousand for Years 2015 through 2023 and % CAGR
- TABLE 235: Mexico 15-Year Perspective for Encoders by Technology - Percentage Breakdown of Value Sales for Optical, Magnetic and Other Technologies for the Years 2015, 2025 & 2030
- REST OF LATIN AMERICA
- TABLE 236: Rest of Latin America Recent Past, Current & Future Analysis for Encoders by Type - Rotary and Linear - Independent Analysis of Annual Sales in US$ Thousand for the Years 2024 through 2030 and % CAGR
- TABLE 237: Rest of Latin America Historic Review for Encoders by Type - Rotary and Linear Markets - Independent Analysis of Annual Sales in US$ Thousand for Years 2015 through 2023 and % CAGR
- TABLE 238: Rest of Latin America 15-Year Perspective for Encoders by Type - Percentage Breakdown of Value Sales for Rotary and Linear for the Years 2015, 2025 & 2030
- TABLE 239: Rest of Latin America Recent Past, Current & Future Analysis for Encoders by End-Use - Medical, Other End-Uses, Industrial, Automotive, Consumer Electronics and Food & Beverage - Independent Analysis of Annual Sales in US$ Thousand for the Years 2024 through 2030 and % CAGR
- TABLE 240: Rest of Latin America Historic Review for Encoders by End-Use - Medical, Other End-Uses, Industrial, Automotive, Consumer Electronics and Food & Beverage Markets - Independent Analysis of Annual Sales in US$ Thousand for Years 2015 through 2023 and % CAGR
- TABLE 241: Rest of Latin America 15-Year Perspective for Encoders by End-Use - Percentage Breakdown of Value Sales for Medical, Other End-Uses, Industrial, Automotive, Consumer Electronics and Food & Beverage for the Years 2015, 2025 & 2030
- TABLE 242: Rest of Latin America Recent Past, Current & Future Analysis for Encoders by Technology - Optical, Magnetic and Other Technologies - Independent Analysis of Annual Sales in US$ Thousand for the Years 2024 through 2030 and % CAGR
- TABLE 243: Rest of Latin America Historic Review for Encoders by Technology - Optical, Magnetic and Other Technologies Markets - Independent Analysis of Annual Sales in US$ Thousand for Years 2015 through 2023 and % CAGR
- TABLE 244: Rest of Latin America 15-Year Perspective for Encoders by Technology - Percentage Breakdown of Value Sales for Optical, Magnetic and Other Technologies for the Years 2015, 2025 & 2030
- MIDDLE EAST
- Encoders Market Presence - Strong/Active/Niche/Trivial - Key Competitors in Middle East for 2025 (E)
- TABLE 245: Middle East Recent Past, Current & Future Analysis for Encoders by Geographic Region - Iran, Israel, Saudi Arabia, UAE and Rest of Middle East Markets - Independent Analysis of Annual Sales in US$ Thousand for Years 2024 through 2030 and % CAGR
- TABLE 246: Middle East Historic Review for Encoders by Geographic Region - Iran, Israel, Saudi Arabia, UAE and Rest of Middle East Markets - Independent Analysis of Annual Sales in US$ Thousand for Years 2015 through 2023 and % CAGR
- TABLE 247: Middle East 15-Year Perspective for Encoders by Geographic Region - Percentage Breakdown of Value Sales for Iran, Israel, Saudi Arabia, UAE and Rest of Middle East Markets for Years 2015, 2025 & 2030
- TABLE 248: Middle East Recent Past, Current & Future Analysis for Encoders by Type - Rotary and Linear - Independent Analysis of Annual Sales in US$ Thousand for the Years 2024 through 2030 and % CAGR
- TABLE 249: Middle East Historic Review for Encoders by Type - Rotary and Linear Markets - Independent Analysis of Annual Sales in US$ Thousand for Years 2015 through 2023 and % CAGR
- TABLE 250: Middle East 15-Year Perspective for Encoders by Type - Percentage Breakdown of Value Sales for Rotary and Linear for the Years 2015, 2025 & 2030
- TABLE 251: Middle East Recent Past, Current & Future Analysis for Encoders by End-Use - Medical, Other End-Uses, Industrial, Automotive, Consumer Electronics and Food & Beverage - Independent Analysis of Annual Sales in US$ Thousand for the Years 2024 through 2030 and % CAGR
- TABLE 252: Middle East Historic Review for Encoders by End-Use - Medical, Other End-Uses, Industrial, Automotive, Consumer Electronics and Food & Beverage Markets - Independent Analysis of Annual Sales in US$ Thousand for Years 2015 through 2023 and % CAGR
- TABLE 253: Middle East 15-Year Perspective for Encoders by End-Use - Percentage Breakdown of Value Sales for Medical, Other End-Uses, Industrial, Automotive, Consumer Electronics and Food & Beverage for the Years 2015, 2025 & 2030
- TABLE 254: Middle East Recent Past, Current & Future Analysis for Encoders by Technology - Optical, Magnetic and Other Technologies - Independent Analysis of Annual Sales in US$ Thousand for the Years 2024 through 2030 and % CAGR
- TABLE 255: Middle East Historic Review for Encoders by Technology - Optical, Magnetic and Other Technologies Markets - Independent Analysis of Annual Sales in US$ Thousand for Years 2015 through 2023 and % CAGR
- TABLE 256: Middle East 15-Year Perspective for Encoders by Technology - Percentage Breakdown of Value Sales for Optical, Magnetic and Other Technologies for the Years 2015, 2025 & 2030
- IRAN
- TABLE 257: Iran Recent Past, Current & Future Analysis for Encoders by Type - Rotary and Linear - Independent Analysis of Annual Sales in US$ Thousand for the Years 2024 through 2030 and % CAGR
- TABLE 258: Iran Historic Review for Encoders by Type - Rotary and Linear Markets - Independent Analysis of Annual Sales in US$ Thousand for Years 2015 through 2023 and % CAGR
- TABLE 259: Iran 15-Year Perspective for Encoders by Type - Percentage Breakdown of Value Sales for Rotary and Linear for the Years 2015, 2025 & 2030
- TABLE 260: Iran Recent Past, Current & Future Analysis for Encoders by End-Use - Medical, Other End-Uses, Industrial, Automotive, Consumer Electronics and Food & Beverage - Independent Analysis of Annual Sales in US$ Thousand for the Years 2024 through 2030 and % CAGR
- TABLE 261: Iran Historic Review for Encoders by End-Use - Medical, Other End-Uses, Industrial, Automotive, Consumer Electronics and Food & Beverage Markets - Independent Analysis of Annual Sales in US$ Thousand for Years 2015 through 2023 and % CAGR
- TABLE 262: Iran 15-Year Perspective for Encoders by End-Use - Percentage Breakdown of Value Sales for Medical, Other End-Uses, Industrial, Automotive, Consumer Electronics and Food & Beverage for the Years 2015, 2025 & 2030
- TABLE 263: Iran Recent Past, Current & Future Analysis for Encoders by Technology - Optical, Magnetic and Other Technologies - Independent Analysis of Annual Sales in US$ Thousand for the Years 2024 through 2030 and % CAGR
- TABLE 264: Iran Historic Review for Encoders by Technology - Optical, Magnetic and Other Technologies Markets - Independent Analysis of Annual Sales in US$ Thousand for Years 2015 through 2023 and % CAGR
- TABLE 265: Iran 15-Year Perspective for Encoders by Technology - Percentage Breakdown of Value Sales for Optical, Magnetic and Other Technologies for the Years 2015, 2025 & 2030
- ISRAEL
- TABLE 266: Israel Recent Past, Current & Future Analysis for Encoders by Type - Rotary and Linear - Independent Analysis of Annual Sales in US$ Thousand for the Years 2024 through 2030 and % CAGR
- TABLE 267: Israel Historic Review for Encoders by Type - Rotary and Linear Markets - Independent Analysis of Annual Sales in US$ Thousand for Years 2015 through 2023 and % CAGR
- TABLE 268: Israel 15-Year Perspective for Encoders by Type - Percentage Breakdown of Value Sales for Rotary and Linear for the Years 2015, 2025 & 2030
- TABLE 269: Israel Recent Past, Current & Future Analysis for Encoders by End-Use - Medical, Other End-Uses, Industrial, Automotive, Consumer Electronics and Food & Beverage - Independent Analysis of Annual Sales in US$ Thousand for the Years 2024 through 2030 and % CAGR
- TABLE 270: Israel Historic Review for Encoders by End-Use - Medical, Other End-Uses, Industrial, Automotive, Consumer Electronics and Food & Beverage Markets - Independent Analysis of Annual Sales in US$ Thousand for Years 2015 through 2023 and % CAGR
- TABLE 271: Israel 15-Year Perspective for Encoders by End-Use - Percentage Breakdown of Value Sales for Medical, Other End-Uses, Industrial, Automotive, Consumer Electronics and Food & Beverage for the Years 2015, 2025 & 2030
- TABLE 272: Israel Recent Past, Current & Future Analysis for Encoders by Technology - Optical, Magnetic and Other Technologies - Independent Analysis of Annual Sales in US$ Thousand for the Years 2024 through 2030 and % CAGR
- TABLE 273: Israel Historic Review for Encoders by Technology - Optical, Magnetic and Other Technologies Markets - Independent Analysis of Annual Sales in US$ Thousand for Years 2015 through 2023 and % CAGR
- TABLE 274: Israel 15-Year Perspective for Encoders by Technology - Percentage Breakdown of Value Sales for Optical, Magnetic and Other Technologies for the Years 2015, 2025 & 2030
- SAUDI ARABIA
- TABLE 275: Saudi Arabia Recent Past, Current & Future Analysis for Encoders by Type - Rotary and Linear - Independent Analysis of Annual Sales in US$ Thousand for the Years 2024 through 2030 and % CAGR
- TABLE 276: Saudi Arabia Historic Review for Encoders by Type - Rotary and Linear Markets - Independent Analysis of Annual Sales in US$ Thousand for Years 2015 through 2023 and % CAGR
- TABLE 277: Saudi Arabia 15-Year Perspective for Encoders by Type - Percentage Breakdown of Value Sales for Rotary and Linear for the Years 2015, 2025 & 2030
- TABLE 278: Saudi Arabia Recent Past, Current & Future Analysis for Encoders by End-Use - Medical, Other End-Uses, Industrial, Automotive, Consumer Electronics and Food & Beverage - Independent Analysis of Annual Sales in US$ Thousand for the Years 2024 through 2030 and % CAGR
- TABLE 279: Saudi Arabia Historic Review for Encoders by End-Use - Medical, Other End-Uses, Industrial, Automotive, Consumer Electronics and Food & Beverage Markets - Independent Analysis of Annual Sales in US$ Thousand for Years 2015 through 2023 and % CAGR
- TABLE 280: Saudi Arabia 15-Year Perspective for Encoders by End-Use - Percentage Breakdown of Value Sales for Medical, Other End-Uses, Industrial, Automotive, Consumer Electronics and Food & Beverage for the Years 2015, 2025 & 2030
- TABLE 281: Saudi Arabia Recent Past, Current & Future Analysis for Encoders by Technology - Optical, Magnetic and Other Technologies - Independent Analysis of Annual Sales in US$ Thousand for the Years 2024 through 2030 and % CAGR
- TABLE 282: Saudi Arabia Historic Review for Encoders by Technology - Optical, Magnetic and Other Technologies Markets - Independent Analysis of Annual Sales in US$ Thousand for Years 2015 through 2023 and % CAGR
- TABLE 283: Saudi Arabia 15-Year Perspective for Encoders by Technology - Percentage Breakdown of Value Sales for Optical, Magnetic and Other Technologies for the Years 2015, 2025 & 2030
- UNITED ARAB EMIRATES
- TABLE 284: UAE Recent Past, Current & Future Analysis for Encoders by Type - Rotary and Linear - Independent Analysis of Annual Sales in US$ Thousand for the Years 2024 through 2030 and % CAGR
- TABLE 285: UAE Historic Review for Encoders by Type - Rotary and Linear Markets - Independent Analysis of Annual Sales in US$ Thousand for Years 2015 through 2023 and % CAGR
- TABLE 286: UAE 15-Year Perspective for Encoders by Type - Percentage Breakdown of Value Sales for Rotary and Linear for the Years 2015, 2025 & 2030
- TABLE 287: UAE Recent Past, Current & Future Analysis for Encoders by End-Use - Medical, Other End-Uses, Industrial, Automotive, Consumer Electronics and Food & Beverage - Independent Analysis of Annual Sales in US$ Thousand for the Years 2024 through 2030 and % CAGR
- TABLE 288: UAE Historic Review for Encoders by End-Use - Medical, Other End-Uses, Industrial, Automotive, Consumer Electronics and Food & Beverage Markets - Independent Analysis of Annual Sales in US$ Thousand for Years 2015 through 2023 and % CAGR
- TABLE 289: UAE 15-Year Perspective for Encoders by End-Use - Percentage Breakdown of Value Sales for Medical, Other End-Uses, Industrial, Automotive, Consumer Electronics and Food & Beverage for the Years 2015, 2025 & 2030
- TABLE 290: UAE Recent Past, Current & Future Analysis for Encoders by Technology - Optical, Magnetic and Other Technologies - Independent Analysis of Annual Sales in US$ Thousand for the Years 2024 through 2030 and % CAGR
- TABLE 291: UAE Historic Review for Encoders by Technology - Optical, Magnetic and Other Technologies Markets - Independent Analysis of Annual Sales in US$ Thousand for Years 2015 through 2023 and % CAGR
- TABLE 292: UAE 15-Year Perspective for Encoders by Technology - Percentage Breakdown of Value Sales for Optical, Magnetic and Other Technologies for the Years 2015, 2025 & 2030
- REST OF MIDDLE EAST
- TABLE 293: Rest of Middle East Recent Past, Current & Future Analysis for Encoders by Type - Rotary and Linear - Independent Analysis of Annual Sales in US$ Thousand for the Years 2024 through 2030 and % CAGR
- TABLE 294: Rest of Middle East Historic Review for Encoders by Type - Rotary and Linear Markets - Independent Analysis of Annual Sales in US$ Thousand for Years 2015 through 2023 and % CAGR
- TABLE 295: Rest of Middle East 15-Year Perspective for Encoders by Type - Percentage Breakdown of Value Sales for Rotary and Linear for the Years 2015, 2025 & 2030
- TABLE 296: Rest of Middle East Recent Past, Current & Future Analysis for Encoders by End-Use - Medical, Other End-Uses, Industrial, Automotive, Consumer Electronics and Food & Beverage - Independent Analysis of Annual Sales in US$ Thousand for the Years 2024 through 2030 and % CAGR
- TABLE 297: Rest of Middle East Historic Review for Encoders by End-Use - Medical, Other End-Uses, Industrial, Automotive, Consumer Electronics and Food & Beverage Markets - Independent Analysis of Annual Sales in US$ Thousand for Years 2015 through 2023 and % CAGR
- TABLE 298: Rest of Middle East 15-Year Perspective for Encoders by End-Use - Percentage Breakdown of Value Sales for Medical, Other End-Uses, Industrial, Automotive, Consumer Electronics and Food & Beverage for the Years 2015, 2025 & 2030
- TABLE 299: Rest of Middle East Recent Past, Current & Future Analysis for Encoders by Technology - Optical, Magnetic and Other Technologies - Independent Analysis of Annual Sales in US$ Thousand for the Years 2024 through 2030 and % CAGR
- TABLE 300: Rest of Middle East Historic Review for Encoders by Technology - Optical, Magnetic and Other Technologies Markets - Independent Analysis of Annual Sales in US$ Thousand for Years 2015 through 2023 and % CAGR
- TABLE 301: Rest of Middle East 15-Year Perspective for Encoders by Technology - Percentage Breakdown of Value Sales for Optical, Magnetic and Other Technologies for the Years 2015, 2025 & 2030
- AFRICA
- Encoders Market Presence - Strong/Active/Niche/Trivial - Key Competitors in Africa for 2025 (E)
- TABLE 302: Africa Recent Past, Current & Future Analysis for Encoders by Type - Rotary and Linear - Independent Analysis of Annual Sales in US$ Thousand for the Years 2024 through 2030 and % CAGR
- TABLE 303: Africa Historic Review for Encoders by Type - Rotary and Linear Markets - Independent Analysis of Annual Sales in US$ Thousand for Years 2015 through 2023 and % CAGR
- TABLE 304: Africa 15-Year Perspective for Encoders by Type - Percentage Breakdown of Value Sales for Rotary and Linear for the Years 2015, 2025 & 2030
- TABLE 305: Africa Recent Past, Current & Future Analysis for Encoders by End-Use - Medical, Other End-Uses, Industrial, Automotive, Consumer Electronics and Food & Beverage - Independent Analysis of Annual Sales in US$ Thousand for the Years 2024 through 2030 and % CAGR
- TABLE 306: Africa Historic Review for Encoders by End-Use - Medical, Other End-Uses, Industrial, Automotive, Consumer Electronics and Food & Beverage Markets - Independent Analysis of Annual Sales in US$ Thousand for Years 2015 through 2023 and % CAGR
- TABLE 307: Africa 15-Year Perspective for Encoders by End-Use - Percentage Breakdown of Value Sales for Medical, Other End-Uses, Industrial, Automotive, Consumer Electronics and Food & Beverage for the Years 2015, 2025 & 2030
- TABLE 308: Africa Recent Past, Current & Future Analysis for Encoders by Technology - Optical, Magnetic and Other Technologies - Independent Analysis of Annual Sales in US$ Thousand for the Years 2024 through 2030 and % CAGR
- TABLE 309: Africa Historic Review for Encoders by Technology - Optical, Magnetic and Other Technologies Markets - Independent Analysis of Annual Sales in US$ Thousand for Years 2015 through 2023 and % CAGR
- TABLE 310: Africa 15-Year Perspective for Encoders by Technology - Percentage Breakdown of Value Sales for Optical, Magnetic and Other Technologies for the Years 2015, 2025 & 2030
- IV. COMPETITION
Pricing
Currency Rates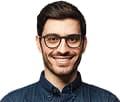